If you make and sell products, you want the best information available for the major decisions you need to make, including setting sale prices for your merchandise. One management strategy that gives you more accurate decision-making information is activity-based costing. This costing practice lets you assign expenses to your products to give you an accurate picture of what it costs to make each individual item of your inventory.
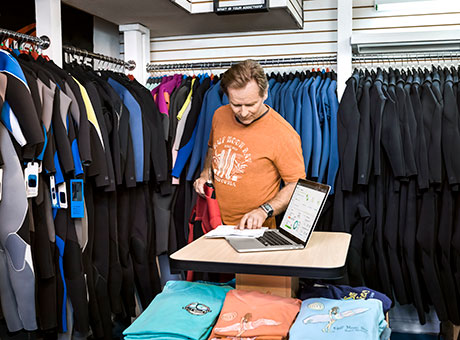
How to Use Activity-Based Costing
Traditional Costing vs. Activity-Based Costing
A traditional costing system uses a flat rate to help distribute expenses that are shared among several product lines. So if you make three products, you might allocate:
- 50% of costs to Product A
- 30% to Product B
- 20% to Product C
If your total monthly expenses are $10,000, $5,000 of this expense is your cost of making Product A.
Activity-based costing lets you use multiple rates for different expenses. Traditional costing groups all your costs together, but that might not be an accurate measure. For example:
- Part of the costs for Products A, B and C include hiring a consultant who spends a total of 10 hours helping you develop all three products.
- Under the traditional costing system, you see 50% of the costs are associated with Product A.
- However, your consultant only spends two hours helping develop that product, which would make allocating 50% of the costs to Product A off balance.
Activity-based costing lets you set a different rate for each type of expense, so you know the exact cost for each product. In the consulting example, 20% of the consultant’s bill goes toward making Product A, instead of 50%. If you use 10% of your office’s square footage to make Product A, you should assign 10% of your rent as a cost of the product. Rather than using one flat rate when assigning costs, you choose multiple rates based on different activities.
Different Cost Drivers Make Activity-Based Costing Work
Cost drivers are variables that explain why costs happen. Activity-based costing works because you choose multiple cost drivers. Going back to the consultant example, the number of hours the consultant works and your office’s square footage are both cost drivers.
Traditional costing systems use just one cost driver. Under activity-based costing, you control how many drivers you use. You make your expense tracking system as complex or simple as you want. That way, you’re more detailed when looking at your costs and you’re getting better information about your goods.
Why Use Activity-Based Costing?
If you can’t directly trace your costs to a product, it’s a good time for activity-based costing. Say you make wooden chairs and dressers and your accountant asks you, “How much does it cost to make a product?
You know the cost of making a chair includes the wood and your labour, but you can’t determine other costs so easily. How much of the overhead cost of your wood glue, nails, paint or finish that you use for both products should you assign to the chair? You don’t have a way of telling exactly how much you used, or maybe it’s not efficient for you to track the costs. You do know that dressers use up more of these materials, so it’s only fair that you assign more of the costs to dressers.
You can’t do this under a traditional costing system. By using an activity-based costing system, you can:
- See what expenses you should assign to your inventory, and
- Figure out a closer estimate of the true cost of each item you sell.
Activity-based costing gives you better information, so you price your goods correctly
Using activity-based costing for your products and having that data handy helps you set the right prices to maximize your profit margins. Keep your books accurate and up-to-date automatically. Change the way you manage your finances with Quickbooks Online now.